Maximize the performance of your wet end.
- Save Resources +
-
Products & Solutions
+
- Rebuilds & Performance
- Dewatering technology
- Machine cleaning and doctoring systems
- Vacuum control systems
- Fabric tensioning and guiding systems
- Consumables and wear parts
- Steam showers and rewetting systems
- Reel change systems
- Machine vision solutions
- Stock, additive and starch preparation
- Monitoring and control technology
- Metering systems
-
Safety
- safetyMASTER
- iSAFETY
back
- Edge and trim handling
-
Tissue Solutions
- Edge and trim handling (Tissue)
- Machine vision solutions
- Machine cleaning and doctoring systems
- Steam showers and rewetting systems
- Safety
- Fabric tensioning and guiding systems
- Vacuum control systems
- Felt suction systems pressMASTER
- Felt suction systems pressMASTER flex
- flowMASTER
- iFIBER deSAVER
- iFIBER deFLAKER
- 3D-Scanning-Service
back
- Services +
- About us +
- Careers +

Optimize fiber composition
Why should you think about it?
The share of fiber costs in total production costs is considerable.
- The cost of fibers accounts for a significant proportion of total production costs.
- The costs and availability of raw materials vary - sometimes greatly.
- High-quality raw materials should be used as selectively as possible.
- The raw material quality of waste paper is continuously decreasing.
How can we support you in this?
With our know-how, our products and solutions, we can support you in optimizing the fiber composition as follows - and all while maintaining or even improving product quality:
- Shift in the composition of raw materials.
- If possible, in the direction of lower-quality, more sustainable raw materials.
- Reduction or shift of basis weight.
- Improvement of the fiber yield in fiber preparation and thus a reduction in reject quantities.
Success Stories
Below you will find a selection of successfully implemented projects.
All projects presented…
- ... show that it is possible to save resources while reducing production cost.
- ... achieved consistent or even improved product quality.
- ... have a return on investment of a few months only taking into account the overall added value achieved.
- ... have been implemented many times - no prototypes or trial installations.
Virgin pulp replaced by recycled fiber.
Savings for project implemented by IBS PPG: € 1,89 Mio. per year
TARGETS ACHIEVED
- Shift in raw material composition while maintaining the same product quality.
- Replacing virgin pulp with waste paper.
- Saving of primary fiber > 3 %.
- Return on investment within a few months.
Long-fiber pulp replaced by short-fiber pulp.
Savings for project implemented by IBS PPG: € 1,7 Mio. per year
TARGETS ACHIEVED
- Shift in raw material composition while maintaining the same product quality.
- Replacement of purchased long-fiber pulp with in-house short-fiber pulp > 8 % or 5,600 t per year.
- Elimination of logistics for the purchased pulp.
- Return on investment within a few months.
Fresh fiber replaced by secondary fiber.
Savings for project implemented by IBS PPG: € 525.000 per year
TARGETS ACHIEVED
- Formation optimization of white top layer and brown bottom layer made it possible to shift basis weight.
- Replacement of virgin fiber with secondary fiber.
- Reduction of B-quality and rejects through general increase in product quality.
- Waiting times for laboratory values such as surface, strength and sheet formation massively reduced.
- Improved product quality.
- Return on investment within a few months.
Fiber yield increased and reject quantities reduced.
Savings for project implemented by IBS PPG: € 280.000 per year
TARGETS ACHIEVED
- Reduction of reject quantities and thus improvement of fiber yield by 980 t/a.
- Waste paper as a raw material is brought into the product and does not have to be discharged.
- This results in a reduced need for reject dewatering (electricity) and logistics for landfill or thermal recycling.
- Same or even improved product quality.
- Return on investment within a few months.
Fresh fiber replaced by converting broke.
Savings for project implemented by IBS PPG: € 1,2 Mio. per year
TARGETS ACHIEVED
- Use of converting broke increased by 50%.
- This replaces virgin fiber with broke.
- Increase in refiner plate service life by 30%.
- 75% reduction of fines in the flotation.
- Equal or even improved product quality.
- Return on investment within a few months.
PAPER
EXPERIENCE
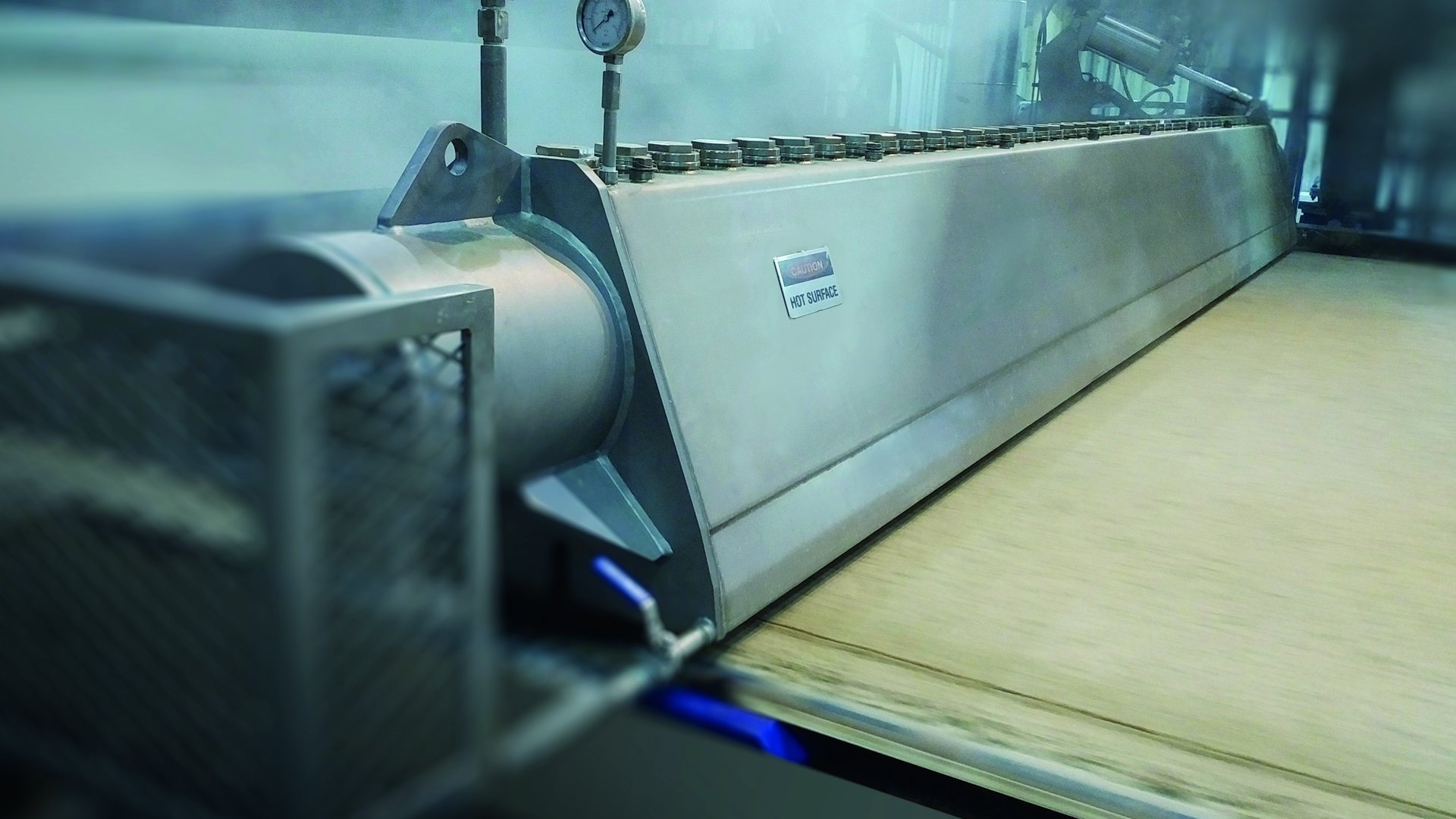
IBS of America Corporation
3732 Profit Way
Chesapeake, VA, 23323
USA
Phone: +1 757-485-4210
E-Mail: Send inquiry