Maximize the performance of your vacuum system.
- Save Resources +
-
Products & Solutions
+
- Rebuilds & Performance
- Dewatering technology
- Machine cleaning and doctoring systems
- Vacuum control systems
- Fabric tensioning and guiding systems
- Consumables and wear parts
- Steam showers and rewetting systems
- Reel change systems
- Machine vision solutions
- Stock, additive and starch preparation
- Monitoring and control technology
- Metering systems
-
Safety
- safetyMASTER
- iSAFETY
back
- Edge and trim handling
-
Tissue Solutions
- Edge and trim handling (Tissue)
- Machine vision solutions
- Machine cleaning and doctoring systems
- Steam showers and rewetting systems
- Safety
- Fabric tensioning and guiding systems
- Vacuum control systems
- Felt suction systems pressMASTER
- Felt suction systems pressMASTER flex
- flowMASTER
- iFIBER deSAVER
- iFIBER deFLAKER
- 3D-Scanning-Service
back
- Services +
- About us +
- Careers +
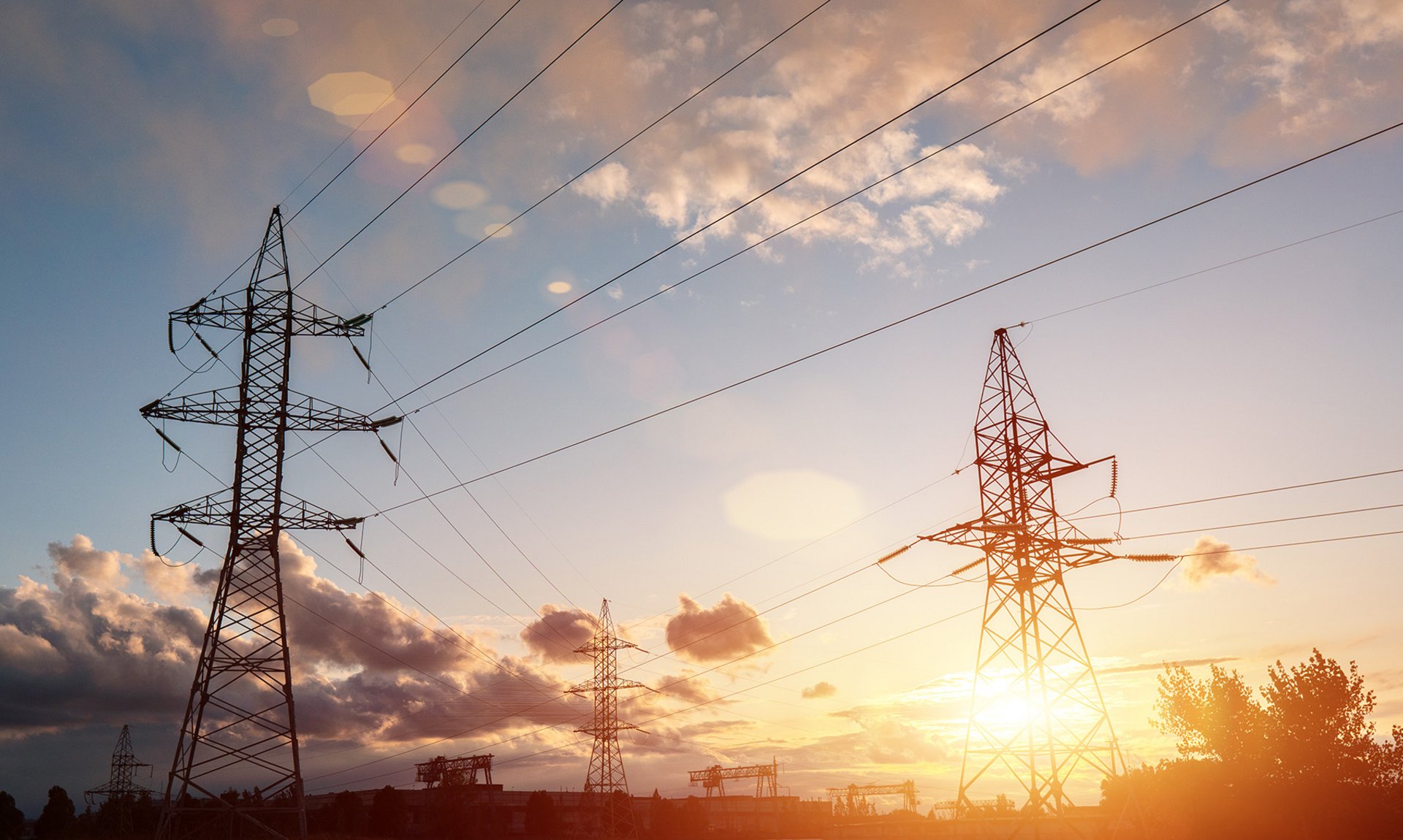
Reduce electricity consumption
Why should you think about it?
The electricity consumption for drives, vacuum supply and other motors is considerable.
- Vacuum sources such as fans, pumps or blowers are major consumers of electrical energy.
- Vacuum is very often not on the radar of paper manufacturers - "it's just there".
- Vacuum and friction are the drivers that influence the amount of drive power required.
How can we support you in this?
With our know-how, products and solutions, we can help you to reduce electricity consumption as follows - and all while maintaining or even improving product quality:
- Optimization of vacuum demand and adaptation to production requirements.
- Optimization of the vacuum curve over the entire wire section.
- Use of automatic valves for reproducibility.
- Re-engineering of the pipelines.
- Reduction of vacuum consumers and therefore vacuum sources.
- Reduction of needed drive power, e.g. through
- Replacement of outdated dewatering systems with modern technology.
- Optimization of dewatering foils and covers with regard to current production conditions (design, material, servicing).
Success Stories
Below you will find a selection of successfully implemented projects.
All projects presented…
- ... show that it is possible to save resources while reducing production cost.
- ... achieved consistent or even improved product quality.
- ... have a return on investment of a few months only taking into account the overall added value achieved.
- ... have been implemented many times - no prototypes or trial installations.
Vacuum pump saved, power consumption reduced.
Savings for project implemented by IBS PPG: € 260.000 per year
TARGETS ACHIEVED
- Reduced power consumption for vacuum supply due to lower vacuum heights.
- This eliminates the need for a 250 kW vacuum pump including necessary maintenance, spare parts, etc..
- Same or even improved product quality.
- Return on investment within a few months.
Power consumption reduced by ultra-high pressure cleaning systems.
Savings for project implemented by IBS PPG: € 80.000 per year
TARGETS ACHIEVED
- Elimination of 180 kW vacuum supply for wire cleaning suction system.
- This results in electricity savings of 1.44 GWh per year.
- Same or even improved product quality.
- Return on investment within a few months.
Drive power and vacuum requirement significantly reduced.
Savings for project implemented by IBS PPG: € 420.000 per year
TARGETS ACHIEVED
- Optimization of dewatering elements (boxes, foils, covers).
- Optimization of vacuum curve over entire wire section.
- Increased dewatering performance by 7%.
- Reduction of total vacuum requirement by 12%.
- Reduction in drive power by 8%.
- Same or even improved product quality.
- Return on investment within a few months.
PAPER
EXPERIENCE
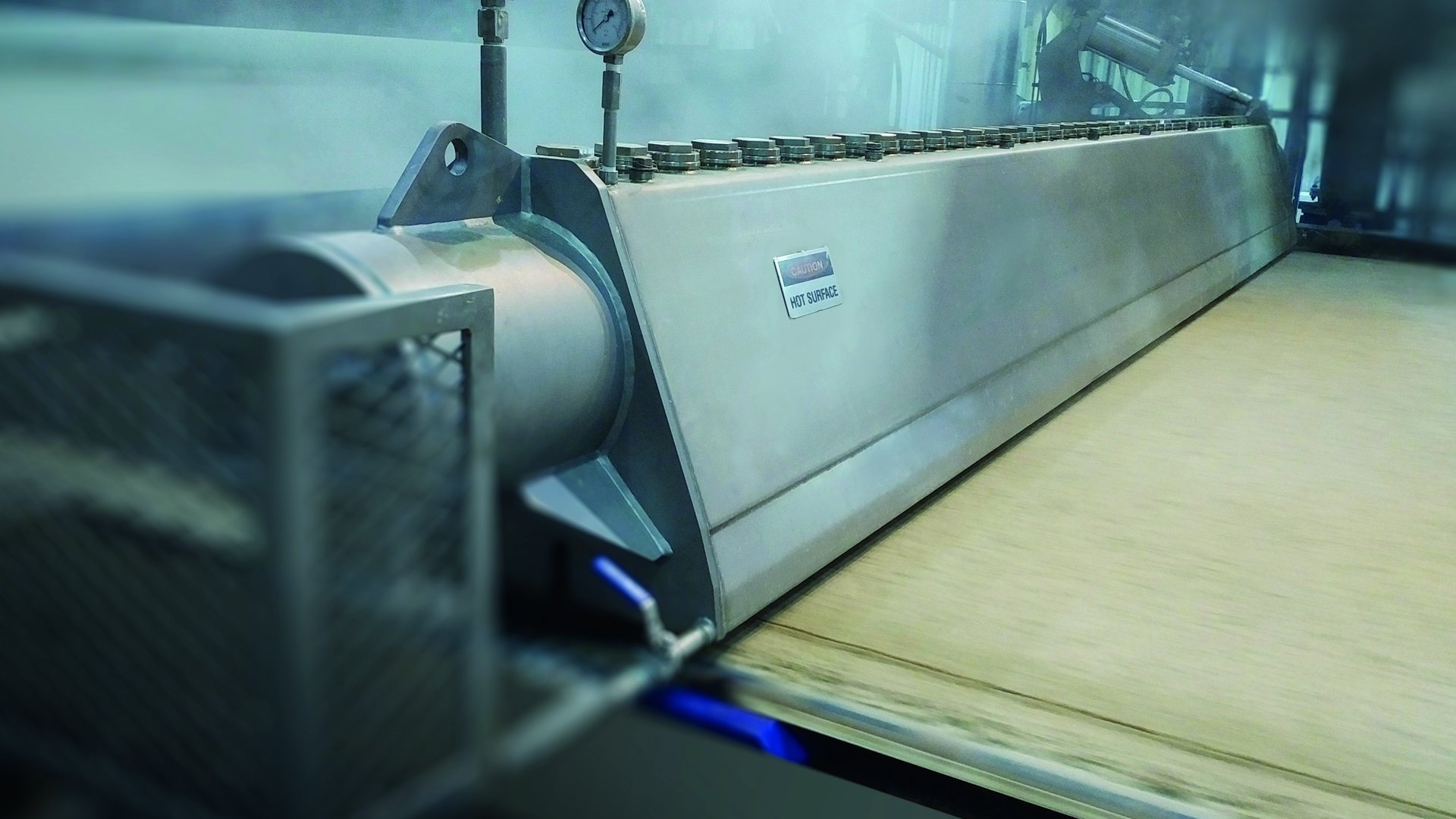
IBS of America Corporation
3732 Profit Way
Chesapeake, VA, 23323
USA
Phone: +1 757-485-4210
E-Mail: Send inquiry